1989年,美國麻省理工學(xué)院發(fā)表了《改變世界的機器》的著名報告,總結(jié)了豐田精益生產(chǎn)方式,指出它的重大歷史意義,并把日本取得成功的生產(chǎn)方式稱為精益生產(chǎn)。精益生產(chǎn)的基本目的是,要在一個企業(yè)里同時獲得極高的生產(chǎn)率、極佳的產(chǎn)品質(zhì)量和很大的生產(chǎn)柔性;消除價值流中的一切七大浪費。
精益生產(chǎn)體系的結(jié)構(gòu)可以簡述為:一個基礎(chǔ)、七個支撐和追求七個“零”的極限目標。
一個基礎(chǔ):即以5S為管理手段的良好現(xiàn)場基礎(chǔ)。所謂5S管理,即整理、整頓、清掃、清潔和素養(yǎng)。
七個支撐:(1)生產(chǎn)的快速換產(chǎn)(SMED)與維護體系;(2)精益品質(zhì)保證與防錯自動化體系;(3)柔性化生產(chǎn)體系;(4)均衡化和同步化體系;(5)現(xiàn)場作業(yè)IE研究體系;(6)生產(chǎn)設(shè)計與高效物流體系;(7)產(chǎn)品開發(fā)設(shè)計體系。
七個極限目標:(1)零切換調(diào)整;(2)零庫存;(3)零浪費;(4)零不良生產(chǎn);(5)零裝備故障;(6)零生產(chǎn)停滯;(7)零安全事故。
日本汽車業(yè)運用豐田精益生產(chǎn)方式,終于超越美國,一躍成為世界第一大汽車生產(chǎn)國。美國通過對日本成功經(jīng)驗的認真總結(jié)和提煉,在實踐中學(xué)習(xí)精益生產(chǎn)方式,也取得了較大的成功,1990年其在北美的市場份額終于超過了日本。
精益生產(chǎn)作為一種新的生產(chǎn)管理模式,在國外汽車制造業(yè)應(yīng)用的成功,引發(fā)了國內(nèi)企業(yè)的興趣,紛紛開始學(xué)習(xí)和嘗試精益生產(chǎn)管理方式。如東風(fēng)汽車集團、一汽集團、躍進汽車集團等。但是國內(nèi)汽車制造業(yè),對精益生產(chǎn)的移植和引入存在一定的片面性,出現(xiàn)了問題,博革咨詢總結(jié)了以下五點問題:
?。?)僅在整車裝配廠部分實現(xiàn)了看板管理取貨制,對下游零部件廠的生產(chǎn)管理并未做更深的擴展和推進。即僅推出了供參觀的樣板廠或樣板車間。
?。?)零部件廠的生產(chǎn)管理多數(shù)依然采用傳統(tǒng)的方式來保證滿足整車廠的需求,缺乏進一步改善生產(chǎn)管理的動力,因此浪費依然大量存在。
?。?)企業(yè)并沒有從完善整個價值流出發(fā)來著手推進精益生產(chǎn),而僅是一種管理工具形式上的改善(如有的企業(yè)就是增加了一些要貨看板)。
(4)盲目照搬國外精益生產(chǎn)的方法和形式,導(dǎo)致了管理紊亂。
?。?)企業(yè)對開展精益生產(chǎn)的漸進性和持久性認識不足。
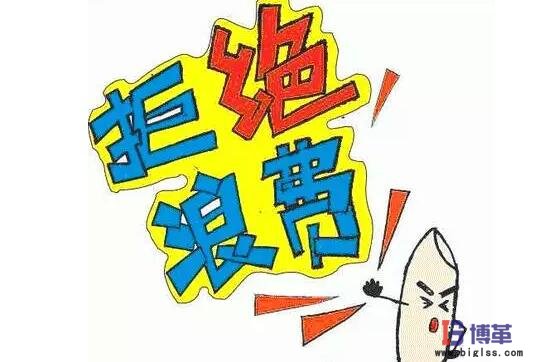
一個基礎(chǔ):即以5S為管理手段的良好現(xiàn)場基礎(chǔ)。所謂5S管理,即整理、整頓、清掃、清潔和素養(yǎng)。
七個支撐:(1)生產(chǎn)的快速換產(chǎn)(SMED)與維護體系;(2)精益品質(zhì)保證與防錯自動化體系;(3)柔性化生產(chǎn)體系;(4)均衡化和同步化體系;(5)現(xiàn)場作業(yè)IE研究體系;(6)生產(chǎn)設(shè)計與高效物流體系;(7)產(chǎn)品開發(fā)設(shè)計體系。
七個極限目標:(1)零切換調(diào)整;(2)零庫存;(3)零浪費;(4)零不良生產(chǎn);(5)零裝備故障;(6)零生產(chǎn)停滯;(7)零安全事故。
日本汽車業(yè)運用豐田精益生產(chǎn)方式,終于超越美國,一躍成為世界第一大汽車生產(chǎn)國。美國通過對日本成功經(jīng)驗的認真總結(jié)和提煉,在實踐中學(xué)習(xí)精益生產(chǎn)方式,也取得了較大的成功,1990年其在北美的市場份額終于超過了日本。
精益生產(chǎn)作為一種新的生產(chǎn)管理模式,在國外汽車制造業(yè)應(yīng)用的成功,引發(fā)了國內(nèi)企業(yè)的興趣,紛紛開始學(xué)習(xí)和嘗試精益生產(chǎn)管理方式。如東風(fēng)汽車集團、一汽集團、躍進汽車集團等。但是國內(nèi)汽車制造業(yè),對精益生產(chǎn)的移植和引入存在一定的片面性,出現(xiàn)了問題,博革咨詢總結(jié)了以下五點問題:
?。?)僅在整車裝配廠部分實現(xiàn)了看板管理取貨制,對下游零部件廠的生產(chǎn)管理并未做更深的擴展和推進。即僅推出了供參觀的樣板廠或樣板車間。
?。?)零部件廠的生產(chǎn)管理多數(shù)依然采用傳統(tǒng)的方式來保證滿足整車廠的需求,缺乏進一步改善生產(chǎn)管理的動力,因此浪費依然大量存在。
?。?)企業(yè)并沒有從完善整個價值流出發(fā)來著手推進精益生產(chǎn),而僅是一種管理工具形式上的改善(如有的企業(yè)就是增加了一些要貨看板)。
(4)盲目照搬國外精益生產(chǎn)的方法和形式,導(dǎo)致了管理紊亂。
?。?)企業(yè)對開展精益生產(chǎn)的漸進性和持久性認識不足。
作者:博革咨詢
推薦新聞